Buick Encore: Diagnostic information and procedures
Brake rotor thickness measurement
SPECIFICATIONS
FASTENER TIGHTENING SPECIFICATIONS
Fastener Tightening Specifications
.jpg)
DISC BRAKE COMPONENT SPECIFICATIONS
Disc Brake Component Specifications
.jpg)
.jpg)
DIAGNOSTIC INFORMATION AND PROCEDURES
BRAKE ROTOR THICKNESS MEASUREMENT
WARNING: Refer to Brake Dust Warning .
- If the inboard friction surface of the brake rotor is not accessible,
reposition and support the caliper with
the brake pads. Refer to Front Disc Brake Pads Replacement.
.gif)
Fig. 1: Micrometer On Brake Rotor
- Clean the friction surfaces of the brake rotor with denatured alcohol,
or an equivalent approved brake
cleaner.
- Using a micrometer (1) calibrated in thousandths-of-a-millimeter, or
ten-thousandths-of-an-inch, measure
and record the thickness of the brake rotor at four or more points, evenly
spaced around the brake rotor.
Make sure that the measurements are only taken within the friction surfaces
and that the micrometer is
positioned the same distance from the outer edge of the brake rotor, about
13 mm (1/2 in), for each
measurement.
- Compare the lowest thickness measurement recorded to the specifications.
Refer to Disc Brake
Component Specifications.
- If the lowest thickness measurement of the brake rotor is above the
minimum allowable thickness after
refinishing specification, the brake rotor may be able to be refinished,
depending upon surface and wear conditions which may be
present.
- If the lowest thickness measurement of the brake
rotor is at or below the discard thickness specification,
the brake rotor requires replacement.
BRAKE ROTOR THICKNESS VARIATION MEASUREMENT
WARNING: Refer to Brake Dust Warning .
NOTE: Any disc brake rotor that exhibits thickness variation
exceeding the maximum
acceptable level must be refinished or replaced. Thickness variation exceeding
the maximum acceptable level can cause brake pulsation.
- If the inboard friction surface of the brake rotor is not accessible,
reposition and support the caliper with
the brake pads. Refer to Front Disc Brake Pads Replacement.
- Clean the friction surfaces of the brake rotor with denatured alcohol,
or an equivalent approved brake
cleaner.
.gif)
Fig. 2: Micrometer On Brake Rotor
- Using a micrometer (1) calibrated in thousandths-of-a-millimeter, or
ten-thousandths-of-an-inch, measure
and record the thickness of the brake rotor at 4 or more points, evenly
spaced around the brake rotor.
Make sure that the measurements are only taken within the friction surfaces
and that the micrometer is
positioned the same distance from the outer edge of the brake rotor, about 13 mm
(1/2 in), for each
measurement.
- Calculate the difference between the highest and lowest thickness
measurements recorded to obtain the
amount of thickness variation.
NOTE: Whenever a brake rotor is refinished or replaced, the
assembled lateral
runout (LRO) of the brake rotor must be measured to make sure optimum
performance of the disc brakes.
- Compare the thickness variation measurement to the following
specification:
Specification
- J93, J94: 0.02 mm (0.0008 in)
- JPW, J97: 0.02 mm (0.0008 in)
- If the brake rotor thickness variation measurement exceeds the
specification, the brake rotor requires
refinishing or replacement.
Brake rotor surface and wear inspection
WARNING: Refer to Brake Dust Warning .
- If the inboard friction surface of the brake rotor is not accessible,
reposition and support the caliper with
the brake pads. Refer to Front Disc Brake Pads Replacement.
- Clean the friction surfaces of the brake rotor with denatured alcohol,
or an equivalent approved brake
cleaner.
- Inspect the friction surfaces of the brake rotor for the following
braking surface conditions:
- Heavy rust and/or pitting
Light surface rust can be removed with an abrasive disc. Heavy surface rust
and/or pitting must be
removed by refinishing the brake rotor.
- Cracks and/or heat spots
- Too much blueing discoloration
- If the friction surfaces of the brake rotor exhibit one or more of the
braking surface conditions, the brake
rotor requires refinishing or replacement.
.gif)
Fig. 3: Micrometer On Brake Rotor
- Using a micrometer (1) calibrated in thousandths-of-a-millimeter, or
ten-thousandths-of-an-inch, measure
and record the scoring depth of any grooves present on the brake rotor
friction surfaces.
- Compare the groove scoring depth recorded to the following specification:
Specification
Brake rotor maximum allowable scoring: 1.50 mm (0.059 in) .
- If the brake disc rotor scoring depth exceeds the specification, or if
an excessive amount of scoring is
present, the brake rotor requires refinishing or replacement.
BRAKE ROTOR ASSEMBLED LATERAL RUNOUT MEASUREMENT
Special Tools
- CH-41013 Rotor Surfacing Kit
- CH-42450-A Wheel Hub Resurfacing Kit
- CH-45101 Hub and Wheel Runout Gauge
- CH-45101-100 Conical Brake Rotor Washers
For equivalent regional tools, refer to Special Tools.
WARNING: Refer to Brake Dust Warning .
NOTE:
- Matchmark the position of the brake rotor to the wheel studs if this has
not been done already.
NOTE: Whenever the brake rotor has been separated from the hub/axle
flange,
any rust or contaminants should be cleaned from the hub/axle flange and
the brake rotor mating surfaces. Failure to do this may result in excessive
assembled lateral runout (LRO) of the brake rotor, which could lead to
brake pulsation.
- Inspect the mating surface of the hub/axle flange and the brake rotor to
make sure that there are no
foreign particles, corrosion, rust, or debris remaining. If the wheel hub/axle
flange and/or brake rotor
mating surfaces exhibit these conditions, perform the following steps:
- Remove the brake rotor from the vehicle. Refer to Front Brake Rotor
Replacement.
- Using the CH-42450-A wheel hub resurfacing kit , thoroughly clean any
rust or corrosion from the
mating surface of the hub/axle flange.
- Using the CH-41013 rotor resurfacing kit , thoroughly clean any rust or
corrosion from the mating
surface of the brake rotor.
- Clean the friction surfaces of the brake rotor with denatured alcohol,
or an equivalent approved
brake cleaner.
- Install the rotor to the hub/axle flange using the matchmark made prior
to removal.
.gif)
Fig. 4: One Lug Nut & Conical Brake Rotor Washers
- Hold the brake rotor firmly in place against the hub/axle flange and
install one of the CH-45101-100
conical brake rotor washers (1), and one lug nut (2) onto the upper-most
wheel stud.
- Continue to hold the brake rotor secure and tighten the lug nut firmly
by hand.
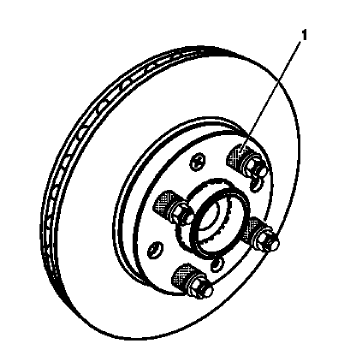
Fig. 5: Wheel Studs
- Install the remaining CH-45101-100 conical brake rotor washers (1) and
lug nuts onto the wheel studs
and tighten the nuts firmly by hand in the tightening sequence.
- Tighten the lug nuts in sequence, in order to properly secure the rotor.
Refer to Tire and Wheel Removal
and Installation .
- If the brake rotor has been REFINISHED or REPLACED with a new rotor,
proceed to step 14.
- If the brake rotor meets the following criteria, proceed to step 10.
- The rotor is within specifications and is being REUSED.
- The rotor has NOT been refinished.
- The rotor does not exhibit thickness variation exceeding the maximum
allowable level.
.gif)
Fig. 6: Hub And Wheel Runout Gauge
- Mount a dial indicator, CH-45101 hub and wheel runout gauge (1), or
equivalent, to the steering knuckle
and position the indicator button so it contacts the brake rotor friction
surface at a 90 degree angle,
approximately 13 mm (0.5 in) from the outer edge of the rotor.
- Measure and record the assembled LRO of the brake rotor:
- Rotate the rotor until the lowest reading is displayed on the indicator
dial, then set the dial to zero.
- Rotate the rotor until the highest reading is displayed on the dial.
- Mark the location of the high spot relative to the nearest wheel stud,
or studs.
- Measure and record the amount of assembled LRO.
- Compare the brake rotor assembled LRO to the following specification:
Specification
Front brake rotor maximum allowable assembled lateral runout: 0.05 mm (0.002
in)
- If the brake rotor assembled LRO is within specifications, proceed to
step 18.
If the brake rotor assembled LRO exceeds the specification, refinish the
rotor to ensure true parallelism.
Refer to Brake Rotor Refinishing. After refinishing the rotor, proceed to step
14.
- Mount a dial indicator, CH-45101 hub and wheel runout gauge , or
equivalent, to the steering knuckle
and position the indicator button so it contacts the brake rotor friction
surface at a 90 degree angle,
approximately 13 mm (0.5 in) from the outer edge of the rotor.
- Measure and record the assembled LRO of the brake rotor.
- Rotate the rotor until the lowest reading is displayed on the indicator
dial, then set the dial to zero.
- Rotate the rotor until the highest reading is displayed on the dial.
- Mark the location of the high spot relative to the nearest wheel stud,
or studs.
- Measure and record the amount of assembled LRO.
- Compare the brake rotor assembled LRO to the following specification:
Specification
Front brake rotor maximum allowable assembled lateral runout: 0.05 mm (0.002
in) .
- If the brake rotor assembled LRO measurement exceeds the specification,
bring the LRO to within
specifications. Refer to Brake Rotor Assembled Lateral Runout Correction.
- If the brake rotor assembled LRO measurement is within specification,
install the brake caliper and
depress the brake pedal several times to secure the brake rotor in place
before removing the CH-45101-
100 conical brake rotor washers and the lug nuts.
Brake pad inspection
.gif)
Fig. 7: Disc Brake Pads And Audible Wear Sensors
WARNING: Refer to Brake Dust Warning .
- Inspect the disc brake pads at regular intervals, or whenever the tire
and wheel assemblies are removed
from the vehicle.
- If replacement is necessary, always replace disc brake pads in axle sets.
- Inspect both edges of the disc brake pad friction surfaces (3). The
highest rate of wear normally occurs at
the trailing edge of the disc brake pads.
- Inspect the thickness of the disc brake pads (3) in order to ensure that
they have not worn prematurely.
The disc brake pad wear should be approximately even per axle set.
- Front brake pads have integral, audible wear sensors (1). When the disc
brake pad wear reaches the
minimum allowable thickness, the wear sensor contacts the disc brake rotor
(2). The wear indicator will
then produce an audible, high-pitched warning noise during wheel rotation.
- Replace the disc brake pads when the friction surface (3) is worn to
within 2.00 mm (0.079 in) of the
mounting plates.
- Verify that any disc brake pad shims that may be required are in place
and not damaged or excessively
corroded. Replace any missing or damaged shims in order to preserve proper
disc brake performance.
- Replace the disc brake pads if any have separated from the mounting
plates.
- Inspect the disc brake pads friction surfaces for cracks, fractures, or
damage which may cause noise or
otherwise impair disc brake performance.
BRAKE CALIPER INSPECTION
.gif)
|
Fig. 8: Brake Caliper Components
WARNING: Refer to Brake Dust Warning .
- Inspect the brake caliper housing (1) for cracks, excess wear, and/or
damage. If any of these conditions
are present, the brake caliper requires replacement.
- Inspect the caliper piston dust boot seal (2) for cracks, tears, cuts,
deterioration and/or improper seating in
the caliper body. If any of these conditions are present, the brake caliper
requires overhaul or
replacement.
- Inspect for brake fluid leakage around the caliper piston dust boot seal
(6) and on the disc brake pads. If
there is any evidence of brake fluid leakage, the brake caliper requires
overhaul or replacement.
.gif)
Fig. 9: Brake Caliper, Inner Brake Pad And C-Clamp
- Inspect for smooth and complete travel of the caliper pistons into the
caliper bores:
- The movement of the caliper pistons into the caliper bores should be
smooth and even. If the
caliper piston is frozen or difficult to bottom, the caliper requires
overhaul or replacement.
- Insert a discarded inner brake pad (2) or block of wood in front of the
piston. Using a large Cclamp
(1) installed over the body of the caliper (3) and against the brake pad or
block of wood,
slowly bottom the piston in the bore.
Front disc brake mounting and hardware inspection
WARNING: Refer to Brake Dust Warning .
.gif)
Fig. 10: Exploded View Of Brake Pads And Brake Caliper Mounting Bracket
- Inspect the fluid level in the brake master cylinder reservoir.
- If the brake fluid level is midway between the maximum-full point and
the minimum allowable level then
no brake fluid needs to be removed from the reservoir before proceeding.
- If the brake fluid level is higher than midway between the maximum-full
point and the minimum
allowable level then remove brake fluid to the midway point before
proceeding.
- Raise and support the vehicle. Refer to Lifting and Jacking the Vehicle
.
- Remove the tire and wheel assembly. Refer to Tire and Wheel Removal and
Installation .
- Grasp the brake caliper housing and try to move the brake caliper
housing up/down and forward/reverse
in relation to the brake caliper mounting bracket (3). If excessive
looseness is observed the brake caliper
bracket bushings and/or the brake caliper mounting bolts may need to be
replaced.
- Compress the front caliper pistons.
- Install a large C-clamp over the top of the caliper housing and against
the back of the outboard pad
(1).
- Slowly tighten the C-clamp until the pistons are pushed completely into
the caliper bores.
- Remove the C-clamp from the caliper.
- With the pistons compressed into the caliper bores, grasp the brake
caliper housing and slide it back and
forth on the brake caliper mounting bolts. Check for smooth operation. If
the brake caliper housing slide force is high or the
brake caliper housing does not slide smoothly, inspect the brake caliper
mounting
bolts and/or the brake caliper mounting bracket bushings for wear or damage.
If wear or damage
conditions are found, replacement of the brake caliper mounting bolts and/or
the brake caliper mounting
bracket bushings is necessary.
- Remove the brake caliper mounting bolts from the
brake caliper mounting bracket and support the brake
caliper using heavy mechanics wire. Do Not remove the hydraulic brake hose
from the caliper. Refer to
Front Brake Caliper Replacement.
- Remove the disc brake pads (1, 4) from the brake
caliper mounting bracket (3).
- Inspect the disc brake pad mounting hardware for the
following:
- Missing mounting hardware.
- Excessive corrosion.
- Bent pad retainer spring (2).
- Looseness at the brake caliper mounting bracket (3).
- Looseness at the disc brake pads (1, 4).
- Excessive contaminants in the brake caliper mounting bracket (3) surface
and threads.
- If any of the conditions listed are found, the disc brake pad mounting
hardware requires replacement.
- Ensure the disc brake pads are held firmly in place on the brake caliper
mounting bracket, yet slide easily
on the mounting hardware without binding.
.gif)
Fig. 11: View Of Caliper, Pin, Boots & Caliper Mounting Bracket
- Inspect the caliper bolts (1) for the following:
- Binding
- Seizing
- Looseness in the brake caliper mounting bracket (3).
- Bent or damaged brake caliper mounting bolts (1).
- Cracked or torn boots (4).
- Missing boots.
- Bent or damaged brake caliper mounting bracket (3).
- Cracked or damaged brake caliper (2).
- If any of the conditions listed are found then the brake caliper
mounting hardware requires replacement.
- Install the disc brake pads to the brake caliper mounting bracket.
- Install the disc brake caliper to the brake caliper mounting bracket.
Refer to Front Brake Caliper
Replacement.
READ NEXT:
Front disc brake pads replacement
Removal Procedure
WARNING: Refer to Brake Dust Warning .
WARNING: Refer to Brake Fluid Irritant Warning .
NOTE: Always replace disc brake pads in axle sets.
Inspect
DISC BRAKE SYSTEM DESCRIPTION AND OPERATION
System Component Description
The disc brake system consists of the following components
Disc Brake Pads
Applies mechanical output force from the hydraulic b
SEE MORE:
What to Use
When the vehicle needs windshield
washer fluid, be sure to read the
manufacturer's instructions before
use. If operating the vehicle in an
area where the temperature may fall
below freezing, use a fluid that has
sufficient protection against
freezing.
Adding Washer Fluid
Open the cap wit
TIRE PRESSURE MONITOR DESCRIPTION AND OPERATION
Tire Pressure Monitoring Block Diagram
Fig. 4: Tire Pressure Monitoring System Wiring Schematic
Special Tools
EL-46079/J-46079 Tire Pressure Monitor Diagnostic Tool
EL-50448 Tire Pressure Monitor Sensor Activation Tool
For equivalent regional